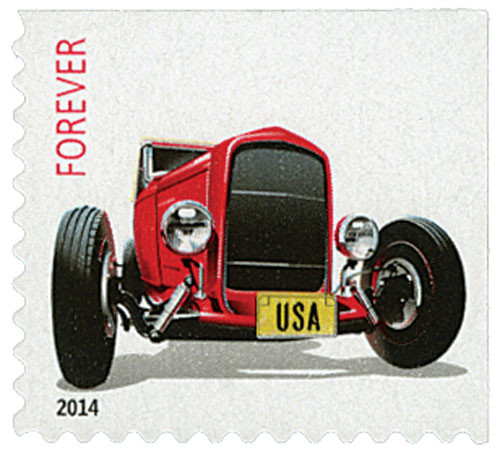
# 4908 - 2014 First-Class Forever Stamp - Hot Rods: Rear of 1932 Ford "Deuce" Roadster
Ford Installs Moving Assembly Line
On December 1, 1913, Henry Ford introduced his moving assembly line, which revolutionized both his own business and the future of mass production around the world.
Henry Ford began his first car making business, the Detroit Automobile Company, in 1899. After two years, it was reorganized as the Henry Ford Company. After disagreements with his partners, Ford left the company. When he found more investors, the Ford Motor Company was established in June 1903. It began making a profit by October. Within two years, the investors had made a profit of almost 300 percent.
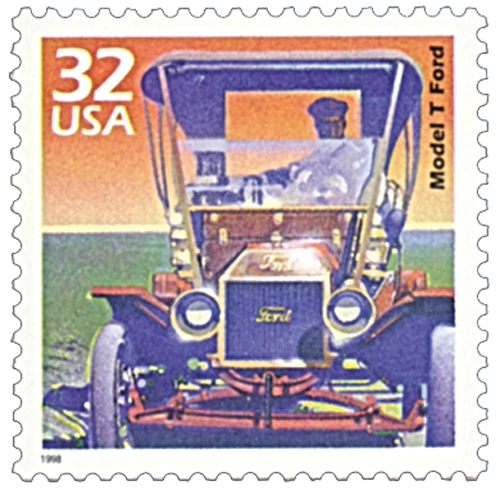
In 1908, Ford introduced the Model T. It was built at a larger factory. Ford’s goal was to produce a car that was so affordable, just about everyone could have one. To accomplish this, he had to decrease the cost and time it took to build his cars. Over the years, he introduced a number of improvements toward this goal. He first split the assembly of the Model T into 84 separate steps and trained each worker to do just one. Ford also built machines that could stamp out the parts faster than human workers were able to. By 1910, demand was so great that Ford moved to the larger Highland Park plant.

Then Ford had a major breakthrough. He’d seen various moving assembly lines at work in flour mills, breweries, canneries, bakeries, and meat-packing plants and believed the same concept could be applied to his factory. Ford experimented with the idea, installing moving lines for some parts of the process. Motors and transmissions were built along rope-and-pulley-powered conveyor belts. When this helped to drastically cut down the production time, Ford decided to expand its use.
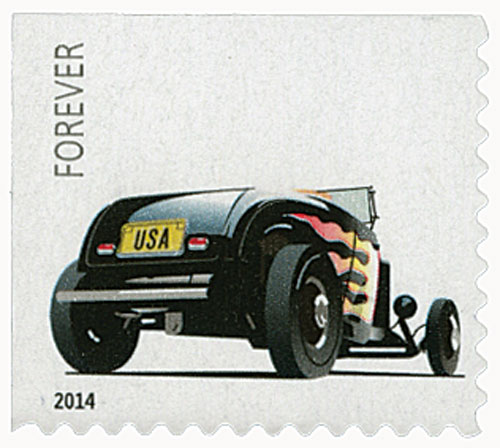
On December 1, 1913, Ford put the moving-chassis assembly line to work. By February, parts were moved past workers on a motorized belt system, allowing the employees to work faster than ever. The 12-and-a-half-hour process of building the Model T was cut down to just one hour and 33 minutes. Ford’s factory produced over 200,000 Model Ts that year, and exceeded one million by 1920. Though Ford didn’t invent the assembly line, he popularized it and soon other car makers and members of other industries began adopting it.
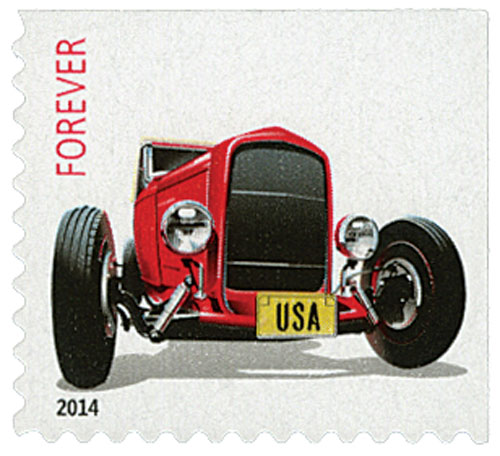
While Ford Motor Company was successful at selling cars, it didn’t fair as well at keeping employees. The turnover rate was high, and the cost of training new workers cut into profits. In January 1914, Ford took a risk and doubled the pay to $5 a day. He also shortened the shifts to eight hours from nine and reduced the work week to five days. Workers stayed at their higher-paying jobs and production increased.
Ford Installs Moving Assembly Line
On December 1, 1913, Henry Ford introduced his moving assembly line, which revolutionized both his own business and the future of mass production around the world.
Henry Ford began his first car making business, the Detroit Automobile Company, in 1899. After two years, it was reorganized as the Henry Ford Company. After disagreements with his partners, Ford left the company. When he found more investors, the Ford Motor Company was established in June 1903. It began making a profit by October. Within two years, the investors had made a profit of almost 300 percent.
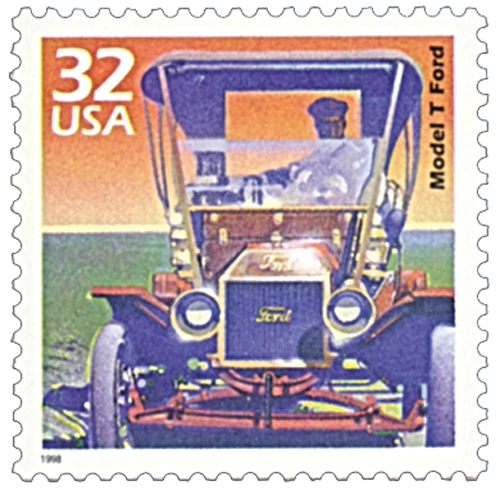
In 1908, Ford introduced the Model T. It was built at a larger factory. Ford’s goal was to produce a car that was so affordable, just about everyone could have one. To accomplish this, he had to decrease the cost and time it took to build his cars. Over the years, he introduced a number of improvements toward this goal. He first split the assembly of the Model T into 84 separate steps and trained each worker to do just one. Ford also built machines that could stamp out the parts faster than human workers were able to. By 1910, demand was so great that Ford moved to the larger Highland Park plant.

Then Ford had a major breakthrough. He’d seen various moving assembly lines at work in flour mills, breweries, canneries, bakeries, and meat-packing plants and believed the same concept could be applied to his factory. Ford experimented with the idea, installing moving lines for some parts of the process. Motors and transmissions were built along rope-and-pulley-powered conveyor belts. When this helped to drastically cut down the production time, Ford decided to expand its use.
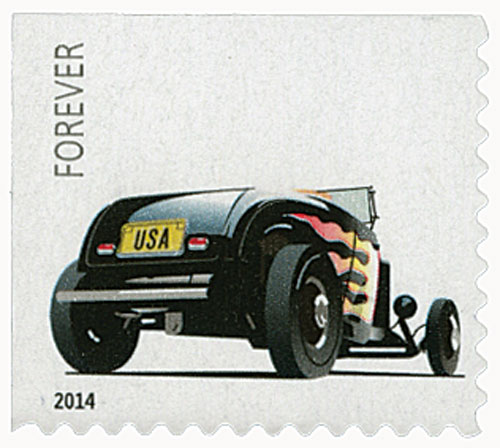
On December 1, 1913, Ford put the moving-chassis assembly line to work. By February, parts were moved past workers on a motorized belt system, allowing the employees to work faster than ever. The 12-and-a-half-hour process of building the Model T was cut down to just one hour and 33 minutes. Ford’s factory produced over 200,000 Model Ts that year, and exceeded one million by 1920. Though Ford didn’t invent the assembly line, he popularized it and soon other car makers and members of other industries began adopting it.
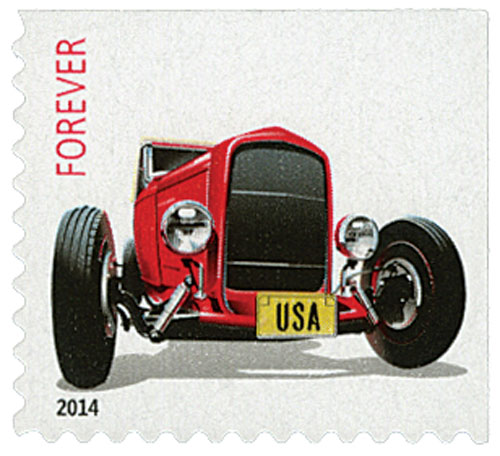
While Ford Motor Company was successful at selling cars, it didn’t fair as well at keeping employees. The turnover rate was high, and the cost of training new workers cut into profits. In January 1914, Ford took a risk and doubled the pay to $5 a day. He also shortened the shifts to eight hours from nine and reduced the work week to five days. Workers stayed at their higher-paying jobs and production increased.